Quote:
Originally Posted by
2Quills http:///forum/thread/376802/415-gallon-plywood-tank-build/960#post_3402664
Looks good. Are you planning on routing it like you did with the slots making more than one pass to get through the material?
Thanks!!!!! Seems such a waste....Made a big jig for 1 cut and now nothing to do with the jig.....Yes that is my game plan from this point out to make several smaller passes with the router than to try to take everything in 1 or 2 big swipes.....I've tried doing big swipes in wood, and it usually doesn't turnout well, so from past experiences, I'm going to practice patience!!!!!!
I did something stupid yesterday in a rush and don't know why???? I was at HD to pick up the MDF since Lowes here doesn't carry full sheets for whatever reason, so I was at HD, and decided I'd pick my bit up there as well to save an extra trip across town....Needless to say I picked up by accident 1/4" shank 1/2" diameter double fluted straight cut bit......Needless to say after 3 passes taking max 1/4" at a shot, I got a bad vibration in the router, and immediately stopped and after close inspection, the router bit self destructed.....I'll have to to get a pic of the bit, if I can dig it out of the trash, but took about 1/2" out of the 1 cutting edge of the bit?????
Pissed to say the least.....All morning I contemplated about returning the 1/4" for 1/2" shank, but finally convinced myself that I'd be alright....Shouldn't have 2nd guessed my thinking.....Needless to say I headed back out to Lowes this time to get a replacement bit; only this time in 1/2" shank.....
Here's the start of the cut process for the eurobracing........
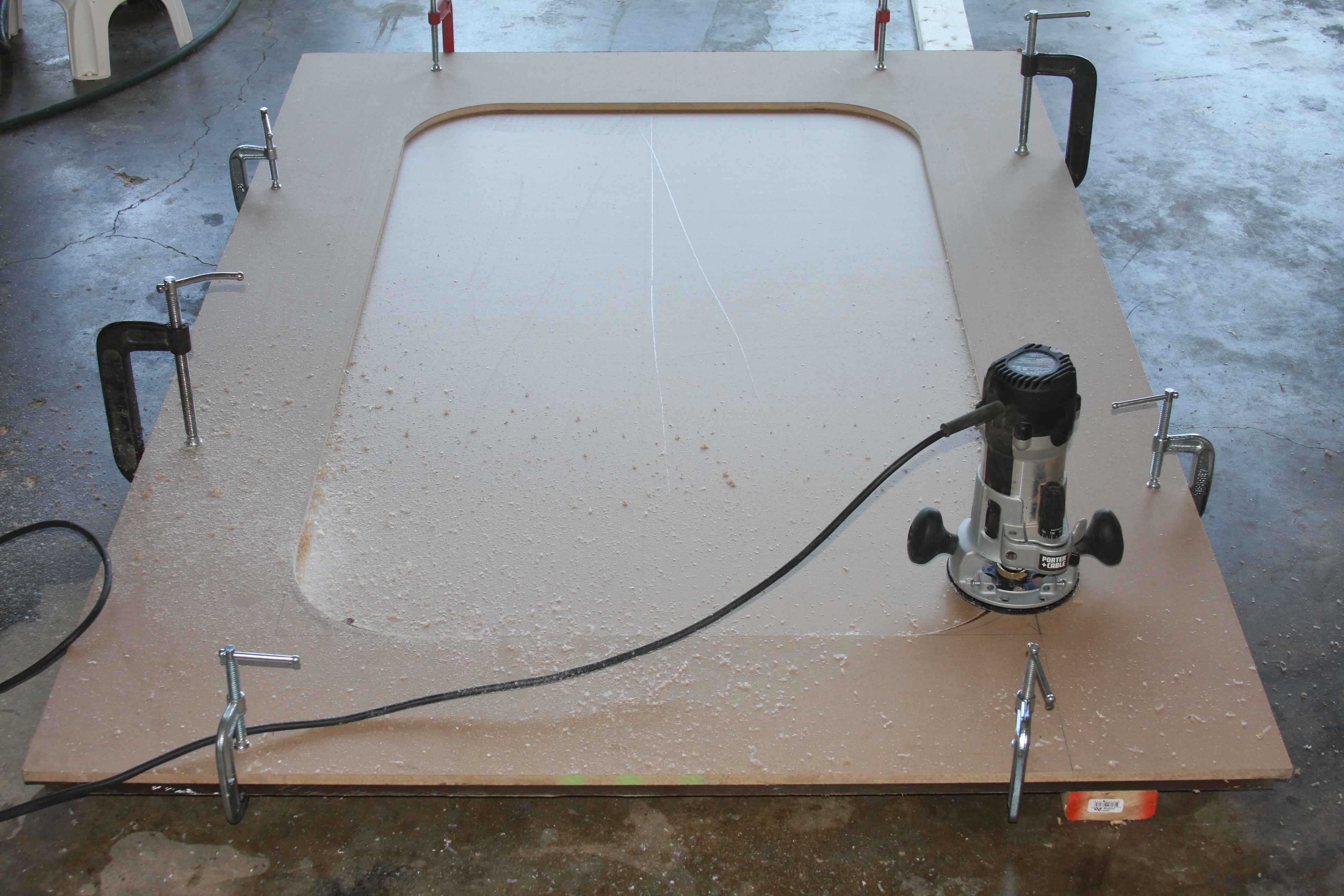
The bad thing about it, I have a big 8' x 4' table off to the right that I could have cleared off, to use, but was to lazy.....So I set 2x4's underneath the acrylic panel with the MDF jig clamped on top......Hats off to Al.....He hinted to me about using my router bushing as my guide.....Worked like a charm Al Thanks!!!!!
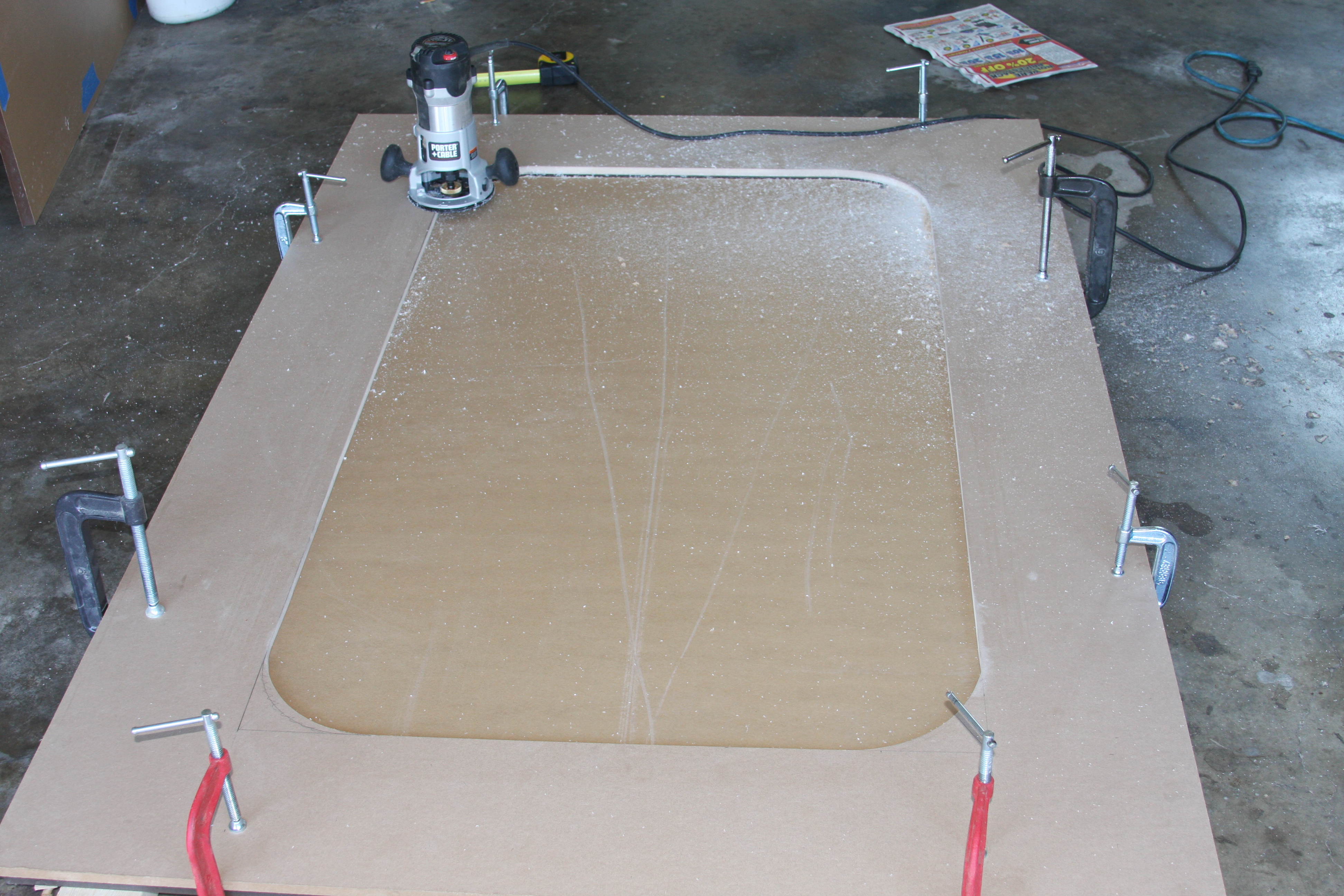
Just another shot.....Thank goodness for Lowes being open late on Sundays.....I did get the eurobracing panel completely cut out.....Once I did my cut through with the straight bit and bushing, I swapped over bits to my flush cut bit, and trimmed it flush to the jig......I'll have to get pics of the completed eurobracing panel tomorrow....Have to get the garage cleaned up and stuff put away....To many piles of shavings all over the floor.....I thought that the panel would really get lighter??? It did, but doesn't seem a whole lot IMO!!!!!!